Building materials and finish selections should be evaluated over the anticipated life span of the project. By evaluating those long-term costs, we are educating ourselves so we can make the correct decisions to keep the house on budget in both the short and long term. A building component, like the fiberglass pilings we recently used for an elevated foundation, cost less in the long run. Despite the higher initial cost compared to traditional timber or concrete piles, the fact that they’re stronger allows us to use fewer of them, reducing the overall cost. They’re also easier to work with and longer lasting since they don’t rot, get eaten by termites or splinter!
Efficient Homes Cost Less in the Long Run
Everyone who gets a power bill knows their power usage patterns and efficiency of the various mechanical systems are directly related to the cost of their utilities. We clean our AC filters, add programmable thermostats and use efficient light bulbs in order to limit the size of our power bills. Still, it’s far less obvious how the cost of construction can relate to the overall, long-term cost of owning a new house.
Simply put, spending a little more on the front end can save big money over the lifespan of a home, especially when selecting construction materials and methods. Specifically, insulation, doors and windows are where most of the expensive leaks and inefficiencies lie. Insulated windows and doors are required by code. A certain amount of insulation is, as well, but the difference between code compliance and what we call “performance construction” can be drastic. Over the long run, an investment in high-efficiency windows, doors and insulation should result in a decrease in the long-term cost of ownership.
Structurally Insulated Panel Systems: Efficiency by Design
In the south, air conditioning costs are the major driver of utility bills and a significant portion of the cost of construction. In order to save on power bills, we should buy efficient air conditioners, but it’s also important to build an efficient structure so that your new super-efficient heat pump isn’t spending half its time cooling or heating air that leaks into and out of your home. To maximize return on the investment from an efficient and expensive air conditioning system, it’s necessary to properly insulate and seal your new or old home.
One of the best ways we’ve found to do this in new construction is by using structurally insulated panel systems, or SIPS. SIPS are a high-performance building material used for structural framing of walls, floors and roofs. They’re constructed from a layer of foam sandwiched between two sheets of plywood or OSB sheathing.
Generally, Structurally Insulated Panel Systems are 6-12” thick and are factory made to exact sizes and shapes. Done correctly, the panels are quick to install, extremely strong, produce very little waste and provide for an incredibly well insulated combination of strength and efficiency. The tight tolerances provided by CAD-designed and computer-cut wall penetrations make it easier to properly seal window and door openings. When assembled with expanding foam or bituminous gasket construction, the level of air infiltration is quantifiably less than traditional construction. In fact, a recently finished SIP house we built was analyzed for leaks and unwanted air infiltration using blower air testing and proved to be 12 times tighter than required by EPA’s Energy Star standards.
Watch for more about SIP construction and air leak testing at the SIPA website.
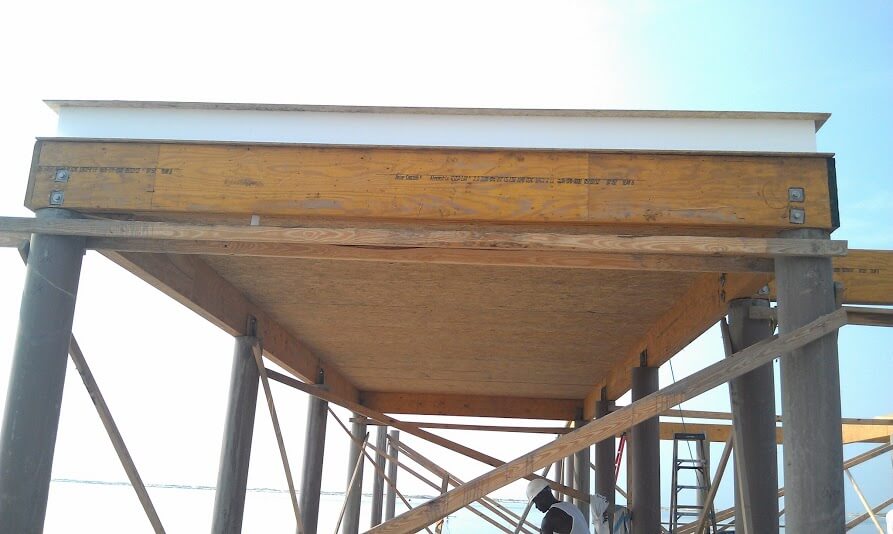
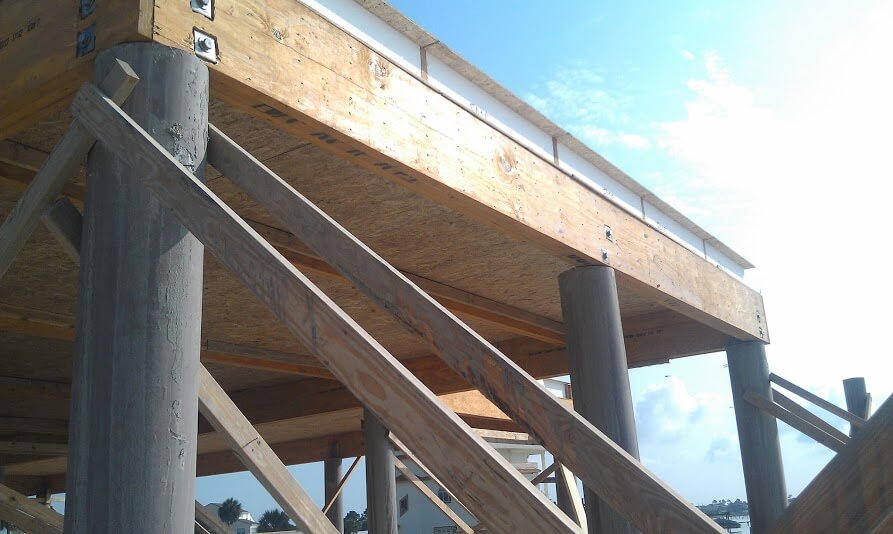
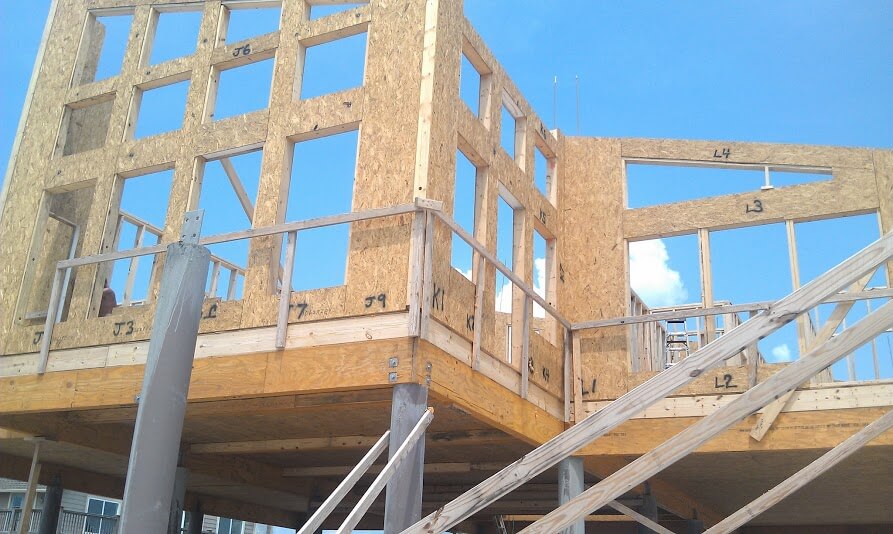
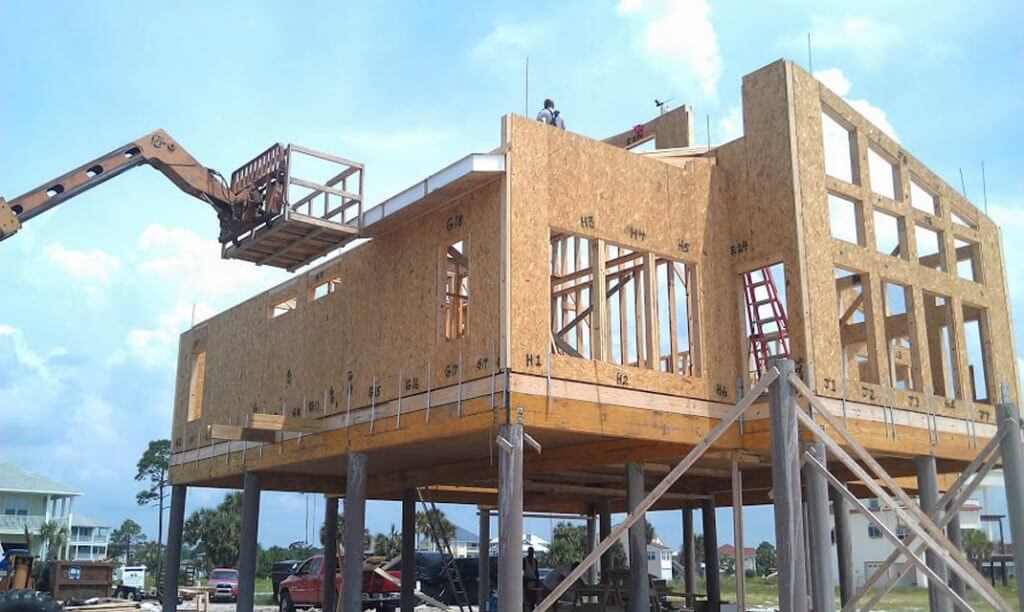
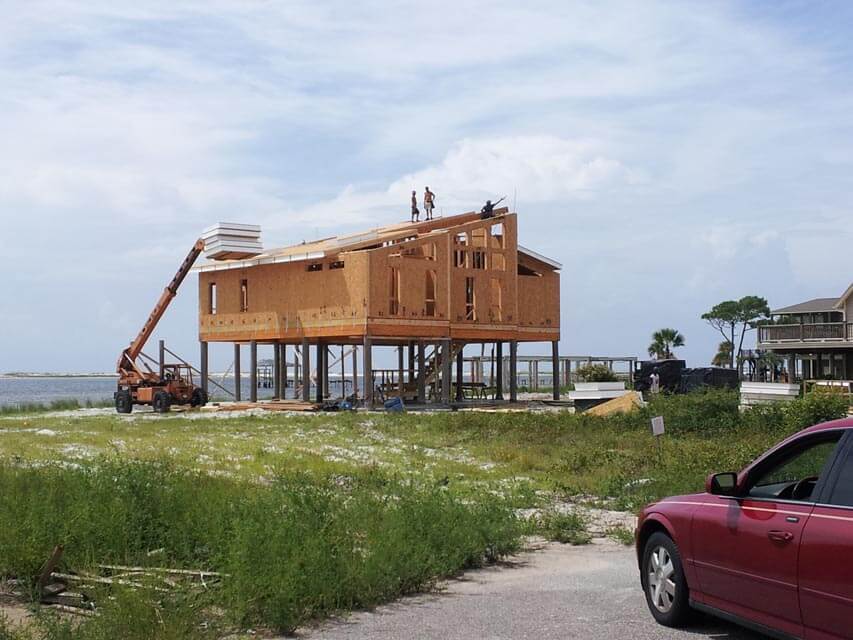